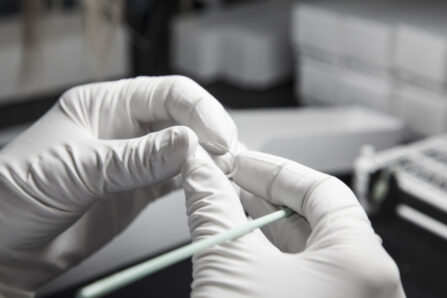
Composants en Saphir
Le saphir, qui est une forme cristalline de l’alumine (Al2O3), fut synthétisé pour la toute première fois il y a plus d’un siècle. Ce n’est que de nos jours que se produisent les avancées les plus spectaculaires associées à ce matériau.
Comadur est la seule société suisse qui possède au sein d’une de ses filiales deux méthodologies de cristallisation de la poudre d’alumine, soit le procédé Verneuil et le procédé EFG (en anglais, Edge defined, Film-fed Growth).
Le saphir synthétique est souvent le matériau de choix pour les ingénieurs devant résoudre des problèmes liés à des applications dans des conditions extrêmes de hautes températures, de hautes pressions et d’environnements chimiques particulièrement corrosifs.
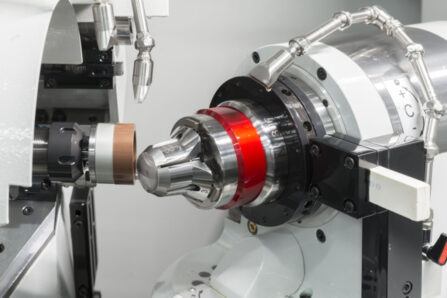
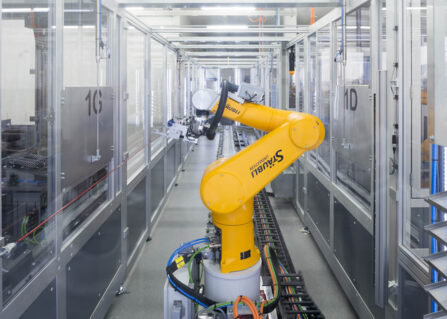
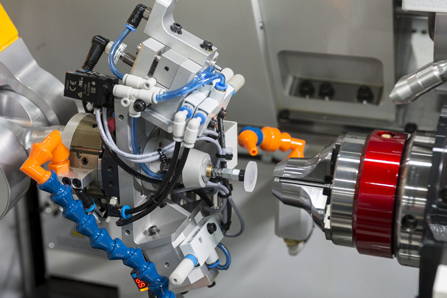
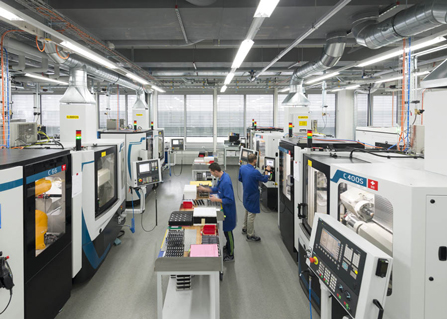
Procédé Verneuil
Ce processus, inventé à la fin du XIXème siècle, porte le nom de son inventeur, Auguste Victor Louis Verneuil, célèbre chimiste français. Il consiste à faire fondre à très haute température, dans une enceinte, de la poudre très fine d’alumine sous une flamme d’hydrogène et d’oxygène.
Les gouttes d’alumine fondue tombent sur un germe de cristal orienté (appelé germe) et finiront par se cristalliser. Au fur et à mesure que la poudre fondue tombe (principe de la stalagmite), la taille du cristal prendra la forme d’une boule de saphir synthétique, dite Verneuil.
Grâce à l’adjonction d’oxyde chrome au sein de la poudre d’alumine, ce procédé est également utilisé pour la croissance de boules de rubis synthétique, matière de base pour la fabrication des rubis d’horlogerie.
Processus EFG
Ce processus, effectué par tirage de plaques à partir d’un bain de saphir fondu est une autre méthode de croissance du saphir synthétique. Cette fois-ci, l’alumine fondue dans un creuset mouille la surface d’une filière et « monte » sous l’effet de l’attraction capillaire. Un germe de saphir d’une cristallinité pure est plongé dans le bain fondu au-dessus de la filière puis retiré très gentiment. Ceci se fait évidemment sous une température minutieusement contrôlée et résulte par une solidification du saphir, lors du tirage, en prenant la forme de la filière.
Le saphir, avec un niveau de 9 sur l’échelle de Mohs, n’est surpassé en dureté et en résistance à la rayure que par le diamant, avec un niveau de 10 sur la même échelle.
Avec son point de fusion à plus de 2’000°C, sa résistance mécanique, sa résistance à l’impact et à la corrosion, sa stabilité dimensionnelle, sa durabilité sous des pressions extrêmes et sa propriété inhabituelle alliant une excellente conductivité thermique à une très haute résistance à la chaleur, tout comme ses propriétés optiques font du saphir un matériau exceptionnel.
Chez Comadur, ce matériau est utilisé pour la fabrication de glaces, de cadrans, de carrures, de lunettes, etc. du domaine horloger, mais aussi pour la fabrication de buses, de paliers, etc. du domaine industriel.
100% de la fabrication de ce matériau extraordinaire, qui rappelons-le, ne peut se faire qu’au-travers d’outils diamantés ou équipements lasers, est verticalisée au sein des différentes usines de Comadur.
Afin d’améliorer encore plus les propriétés optiques des composants en saphir, nous possédons, chez Comadur, plusieurs technologies d’anti-reflet qui nous permettent de déposer de très fines couches successives, très dures, à la surface dudit composant.
Pour répondre aux attentes les plus exceptionnelles des designers, des éléments de décoration, comme la dépose de couches métallisées ou ITO, le gravage intra-saphir, l’incrustation de matériaux nobles, etc. ont été développés par nos ingénieurs/-es R&D et sont des procédés que nous maîtrisons intégralement au sein de notre production.
Composants en Céramique
Les céramiques sont des matériaux non métalliques et non organiques obtenus par l’action de très hautes températures, mais en-dessous de leur température de fusion, ce qui les distingue du saphir synthétique, qui est lui obtenu par fusion de poudre d’alumine.
Ces fortes températures induisent au cœur de la matière première, une transformation irréversible qui confère à la matière des propriétés exceptionnelles, par ex. résistance mécanique, résistance aux chocs, résistance à la chaleur, propriétés isolantes, etc. Ces processus sont appelés communément frittage et se déroulent à des températures entre 1’400°C et 1’600°C, ceci en fonction de la nature du matériau.
LIRE LA SUITE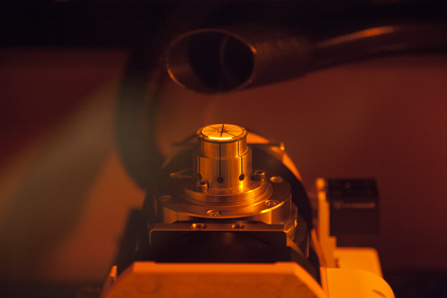
Chez Comadur, grâce aux connaissances techniques et au savoir-faire de nos ingénieurs R&D en matériaux « durs », nous avons développé plusieurs familles de céramiques, à base d’alumine, de zircone, de nitrure de titane, de carbure de titane, de nitrure de silicium, etc. De plus, afin de répondre aux spécificités du domaine horloger, nous avons mis au point plus de 30 couleurs de céramiques, toutes disponibles de manière industrielle.
100% de la fabrication de ces matériaux exceptionnels est verticalisée au sein des différentes usines de Comadur. Les composants issus de notre production possèdent non seulement des propriétés physiques hors du commun mais également des finitions esthétiques remarquables car nous maîtrisons l’ensemble de la supply-chain, depuis l’approvisionnement des poudres au produit fini.
Les matériaux en céramique sont utilisés pour la fabrication de tout composant d’habillage horloger, mais aussi pour la fabrication de buses, de paliers, de roues dentées, d’isolateurs, etc. du domaine industriel.
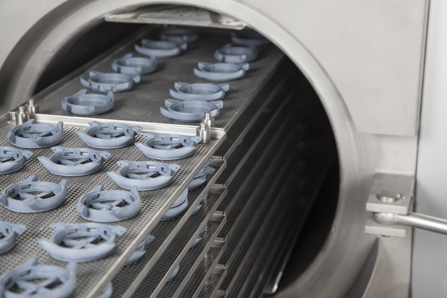
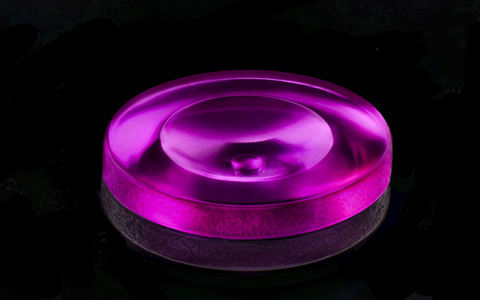
Pierres Horlogères
Ce n’est qu’au début du XVIIIème siècle, que l’astronome et opticien suisse Nicolas Fatio de Duillier, installé à Londres, découvre le moyen de percer des rubis naturels pour les utiliser dans la fabrication des mouvements d’horlogerie.
Cependant, ce n’est qu’en 1902, que le célèbre chimiste français Auguste Victor Louis Verneuil communiqua à l’Académie des sciences cette phrase : « du point de vue chimique, physique et cristallographique, il y a une identité de propriétés et de structures moléculaires entre le rubis de fusion (synthétique) et le rubis naturel ».
Dans la pratique, les rubis synthétiques présentent des avantages décisifs sur les rubis naturels, puisque « l’imitation » surpasse l’original notamment en ce qui concerne ses applications industrielles.
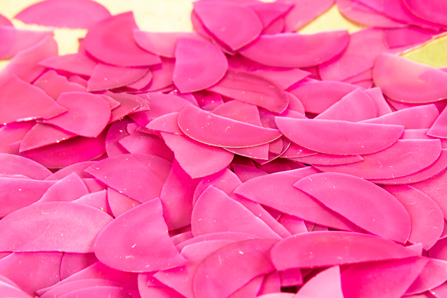
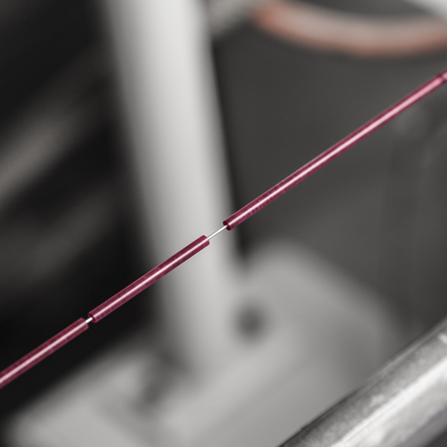
Tout comme pour la croissance du saphir, Comadur possède ses propres rampes Verneuil destinées à la fabrication de rubis synthétique. Avec le saphir, ce dernier est le matériau le plus dur (niveau 9 sur l’échelle de Mohs) après le diamant, avec un niveau de 10 sur la même échelle.
Le processus Verneuil consiste à faire fondre à très haute température (> 2’000°C), dans une enceinte, de la poudre d’alumine mélangée avec de l’oxyde de chrome sous une flamme d’hydrogène et d’oxygène.
Les gouttes d’alumine fondue tombent sur un germe de cristal orienté (appelé germe) et finiront par se cristalliser. Au fur et à mesure que la poudre fondue tombe (principe de la stalagmite), la taille du cristal prendra la forme d’une petite boule de rubis synthétique, qui deviendra la matière de base pour la fabrication des rubis d’horlogerie.
Avec son point de fusion à plus de 2’000°C, sa résistance mécanique, sa résistance à l’impact et à la corrosion, sa stabilité dimensionnelle, sa durabilité sous des pressions extrêmes font du rubis un matériau exceptionnel.
Chez Comadur, ce matériau est utilisé pour la fabrication des pierres et levées d’horlogerie, mais aussi pour la fabrication de buses, de paliers, etc. du domaine industriel. Au sein d’un mouvement horloger, la principale caractéristique des composants en rubis est de minimiser le frottement entre la pierre et l’axe du mobile qui est généralement métallique.
100% de la fabrication de ce matériau qui ne peut se faire qu’au-travers d’outils diamantés ou équipements lasers, est verticalisée au sein des différentes usines de Comadur. Une multitude de géométries et de finitions font partie de notre catalogue standard de production.
Micro-aimants
Les micro-aimants fabriqués par Comadur sont réputés pour leur précision, pour leur qualité et pour leur reproductibilité irréprochable. Maîtrisant le savoir-faire très délicat de la fabrication des micro-aimants en terres rares, Comadur a développé d’ingénieux procédés permettant à cette ligne de produits d’être utilisés au sein des moteurs pas-à-pas des mouvements à quartz de l’horlogerie suisse, les plus précis au monde.
Les micro-aimants sont fabriqués à partir d’une poudre qui, une fois compactée, subit une opération de frittage. Quelques opérations d’usinage et de polissage viennent finalement parfaire nos micro-aimants horlogers.
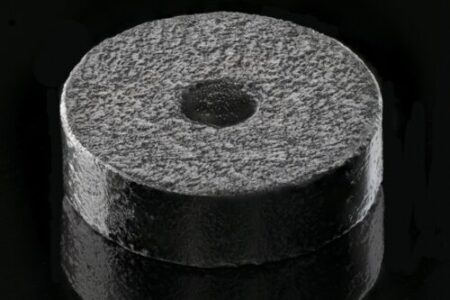
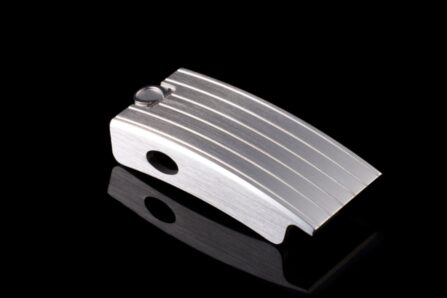
Composants Métalliques
Avec la volonté d’offrir à nos clients les matériaux les plus durs, Comadur a décidé de développer la fabrication de composants d’habillage en acier inoxydable sans nickel. Ce matériau, dont la composition est brevetée, présente une résistance accrue aux frottements grâce à une dureté de plus de 300 Vickers, égalant celle des titanes. Ce grade d’acier inoxydable, de sa composition, est par ailleurs non allergène, amagnétique et doté d’une excellence tenue à la corrosion.
Grâce à des traitements thermiques spécifiques, spécialement élaborés par nos ingénieurs, ces derniers permettent d’élaborer tous types de terminaisons (polissage, satinage, etc.)