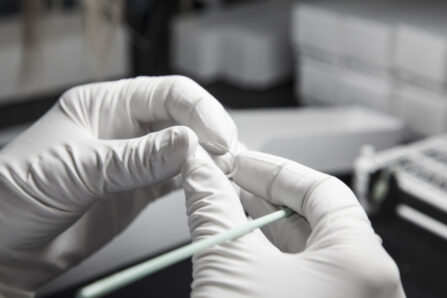
Sapphire components
Sapphire, a crystallised form of alumina (Al2O3), was first synthetised more than a century ago. However, the most spectacular breakthroughs involving this material have only been made recently.
Comadur is the only Swiss company with a site that has two methods for crystallising alumina powder, namely the Verneuil process and the EFG (edge-defined, film-fed growth) process.
Synthetic sapphire is often the material of choice for engineers seeking to resolve issues relating to applications in extreme conditions such as in high temperatures, under high pressure, and in particularly corrosive chemical environments.
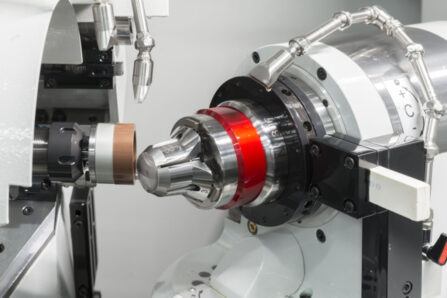
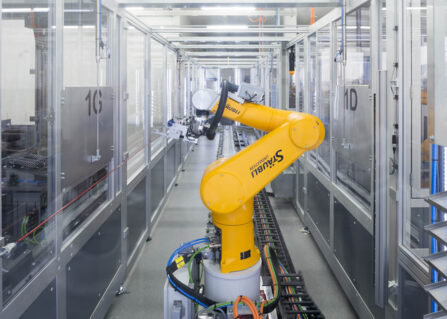
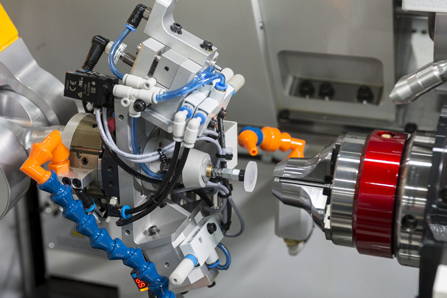
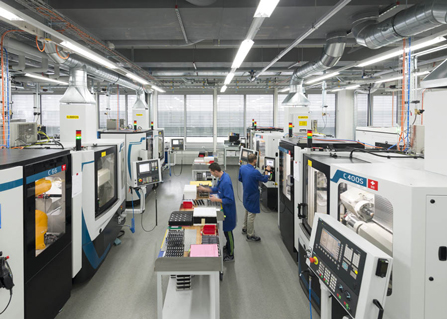
Verneuil process: This process, invented at the end of the 19th century, bears the name of its inventor Auguste Victor Louis Verneuil, a famous French chemist. It consists of melting very fine alumina powder in a container at a very high temperature over an oxyhydrogen flame.
The drops of melted alumina fall onto a seed crystal and ultimately crystallise. As the melted powder falls (stalagmite principle), the growing crystal takes the shape of a mass of synthetic sapphire known as a Verneuil boule.
If chromium oxide is added to the alumina powder, this process can also be used to grow synthetic ruby boules, the raw material needed to make watchmaking rubies.
EFG process: This process, performed by drawing out a layer of film from a tub of melted sapphire, is another method of growing synthetic sapphire. Here, the alumina is melted in a crucible and coats the surface of a shaper, and ‘rises’ under the effect of capillary attraction. A pure crystalline seed sapphire is immersed in the molten liquid above the shaper then very carefully removed. This is of course done at meticulously controlled temperatures and results in the sapphire solidifying when drawn out and taking the form of the shaper.
At level 9 on the Mohs scale, sapphire is harder and more resistant to scratching than any other mineral apart from diamond, which comes in at 10 on the same scale.
Sapphire is an exceptional material thanks to its melting point of more than 2,000°C, mechanical strength, impact and corrosion resistance, dimensional stability, durability under extreme pressure, and unusual properties combining excellent thermal conductivity with high resistance to heat, as well as its visual properties.
At Comadur, this material is used to make crystals, dials, middle sections, bezels and so on for the watchmaking industry, as well as to produce nozzles, bearings and other items for the industrial sector.
100% of the production process for this extraordinary material, which (it is worth noting) requires diamond tools or laser equipment, is integrated vertically into Comadur’s various factories.
To further improve the visual characteristics of sapphire components, at Comadur we have various anti-glare technologies that enable us to apply a series of very thin, very hard layers to the surface of the component.
To meet even the most exceptional requests from designers, various decorative elements – including metallic or ITO layers, intra-sapphire engraving, and high-grade material inlaying – have been developed by our R&D engineers and transformed into processes that we can fully incorporate into our production.
Ceramic components
Ceramics are non-metallic, non-organic materials produced under the action of temperatures that are very high but below the material’s melting point, setting them apart from synthetic sapphire, which is obtained by melting alumina powder.
Within the raw material, these high temperatures trigger an irreversible transformation that gives the material exceptional properties such as mechanical strength, shock resistance, heat resistance and insulating properties. These processes are collectively known as ‘sintering’ and take place at temperatures between 1,400°C and 1,600°C, depending on the type of material.
READ MORE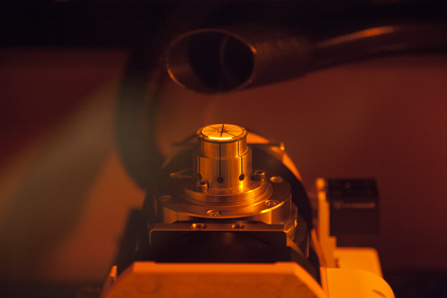
At Comadur, our R&D engineers’ technical knowledge and expertise in ‘hard’ materials have enabled us to develop various families of ceramics made from alumina, zirconia, titanium nitride, titanium carbide, silicon nitride and other substances. In addition, in order to meet the specific needs of the watchmaking sector, we have perfected more than 30 ceramic colours all available for industrial use.
100% of the production process for these exceptional materials is integrated vertically into Comadur’s various factories. As well as having exceptional physical properties, the components we produce also offer remarkable aesthetic finishes, as we have control of the entire supply chain from powder procurement through to the finished product.
Ceramic materials are used in the production of external watchmaking components, as well as in the manufacture of nozzles, bearings, gear wheels, insulators and other items for the industrial sector.
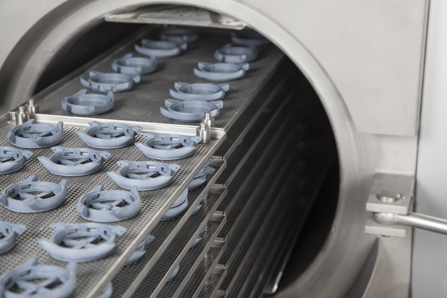
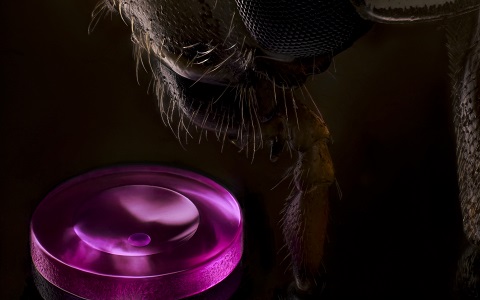
Watchmaking jewels
Swiss astronomer and optician Nicolas Fatio de Duillier, who was based in London, first discovered a method of piercing natural rubies for use in producing watchmaking movements in the early 18th century.
However, it was not until 1902 that the famous French chemist Auguste Victor Louis Verneuil informed the Académie des Sciences that ‘from a chemical, physical and crystallographic perspective, there is a similarity between the properties and molecular structures of synthetic and natural rubies.’
In practice, synthetic rubies offer some key advantages over natural rubies, with the ‘imitation’ outperforming the original when it comes to industrial applications in particular.
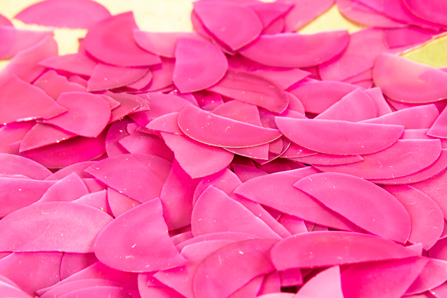
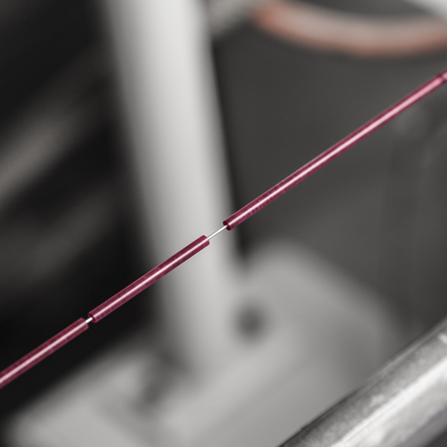
As it does for growing sapphire, Comadur also has its own Verneuil ramps for producing synthetic ruby. Along with sapphire, this is the hardest material (at 9 on the Mohs scale) after diamond (which comes in at level 10).
The Verneuil process consists of melting alumina powder mixed with chromium oxide in a container at a very high temperature (> 2,000°C) over an oxyhydrogen flame.
The drops of melted alumina fall onto a seed crystal and ultimately crystallise. As the melted powder falls (stalagmite principle), the growing crystal takes the shape of a small boule of synthetic ruby, which becomes the base material for producing watchmaking rubies.
Ruby is an exceptional material thanks to its melting point of more than 2,000°C, mechanical strength, impact and corrosion resistance, dimensional stability, and durability under extreme pressure.
At Comadur, this material is used to make watchmaking jewels and impulses, as well as to produce nozzles, bearings and other items for the industrial sector. Within a watchmaking movement, the main role of ruby components is to minimise friction between the jewel and the wheel shaft, which is generally made of metal.
100% of the production process for this material, which requires diamond tools or laser equipment, is integrated vertically into Comadur’s various factories. Our standard production catalogue includes a wide range of geometries and finishes.
Micro-magnets
The micro-magnets made by Comadur are renowned for their precision, quality, and impeccable reproducibility. Having mastered the very delicate skill of producing rare-earth micro-magnets, Comadur then developed some ingenious processes that enable this line of products to be used in stepping motors for quartz movements in the Swiss watchmaking industry, the most precise such motors in the world.
Micro-magnets are made from a powder that is compacted and then subjected to friction. Our watchmaking micro-magnets are then perfected with machining and polishing operations.
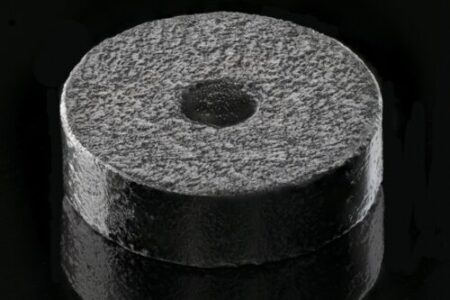